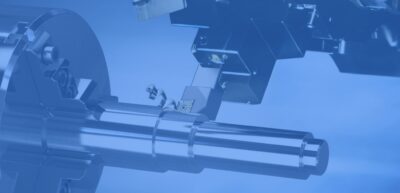
How Markforged is Revolutionizing Cost Savings at Danone Dairy Plant
Written by | Prableen Sachdeva
June 24, 2024
| 10:23 am
Discover how Markforged 3D printing is revolutionizing cost savings at the Danone dairy plant in Bieruń, Poland. Learn how they achieved an impressive 80% cost reduction across 374 parts, including a custom-designed vacuum gripper that’s transformed their production line. Explore the benefits of on-demand part creation, minimized downtime, and rapid return on investment that Markforged’s technology delivers